This week, we hosted a building session for our team so that we were able to implement many of the previously described design criteria. This build session included the addition of the speed controller, the removal of the doors of the vehicle, the introduction of an acceleration button on the steering wheel, and a total redesigned steering system.
The speed controller was introduced so that the therapist would be able to alter the speed of the car according the needs of each child. This device allows the car to operate at a full range of speeds, from maximum speed to an almost unnoticeable crawl. The speed controller works by introducing a variable resistor into the circuitry of the car, and the knob of the potentiometer changes the amount of voltage applied to the motor. The speed controller device was placed underneath the seat alongside the battery for safety purposes, while the adjustment knob was placed outside of the vehicle for easy access.
The doors were removed from the vehicle to allow easy access for students as they entered and exited the vehicle. The doors were found not to be integral to the structure of the vehicle, and could be added back at a later date if deemed necessary by a therapist.
The acceleration button on the steering wheel was necessary for students who may not have the motor control abilities in their legs necessary. A hole was drilled out of the steering wheel so that a large, round button could be inserted. Next, the wires from the button were introduced into the existing circuitry of the car so that either the hand button or the floor pedal could act as the switch to accelerate the vehicle.
The redesigned steering system addressed two needs. First it allows easier steering through a “handlebar” approach rather than the typical small steering wheel. Next, it but be able to be pushed so that it activates the hand pedal. The design accomplishes both of these needs by attaching a length of PVC pipe above the existing steering wheel and hand button using compressible foam. Therefore, when the handlebar is pressed, it also compresses onto the hand pedal, accelerating the car. This system will be fortified using metal U-brackets to ensure proper steering and durability.
Also, we met with an occupational therapist student at Belmont named Alyssa wo gave us many ideas on the design for the seat of the vehicle. She recommended that we use an adjustable frame built with PVC so that ample structure support would be provided for the kids, while adjustability could be maintained. She also mentioned the need for lateral support, which could be accomplished though robust sidewalls on the vehicle. Finally, she stressed the importance of maintaining a proper length for the distance from the seat to the steering wheel so that students would be able to reach the steering wheel without straining. She is excited about the opportunity to use our vehicle with the students and report back to us the efficacy of our design.
We received another shipment of parts this week. We received our 5-point harness, the forearm tray, and the parts required to build the adjustable tray. We are hosting another build session this week, and will report the success of the implementation of these parts at a later date.
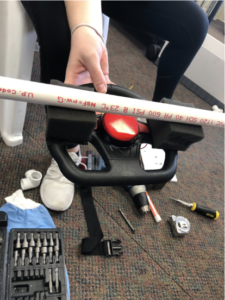