High Fidelity Reduced Order Modeling of Polycrystalline Materials
Research Sponsor:
Air Force Office of Scientific Research, Multi-Scale Structural Mechanics and Prognosis. Program Director: Dr. David Stargel.
Research Goal and Objectives
Goal:
Prediction of damage initiation, accumulation and failure in Ti6242S structures subjected to extreme environment for design and sustainment of in-atmosphere, reusable, hypersonic flight platforms
Specific Objectives:
Develop computational modeling and simulation infrastructure with the ability to predict Ti6242S structures limit states when subjected to high temperatures, time varying and high amplitude thermal and pressure loads.
Assess validity of the computational methods and models based on high-fidelity analysis methods and experimental investigations for assessment of computational efficiency so that large structural simulations are possible and accuracy for capturing the pertinent life limiting mechanisms.
Predict damage accumulation and failure by exercising the computational framework to gain fundamental understanding of structural response when subjected to extreme thermo-mechanical environments and variable amplitude load histories.
Research Impact:
Enables design of hypersonic structures through reduction of the high knockdown factors used to compensate for the lack of knowledge of damage accumulation mechanisms.
Enables cost-efficient sustainment protocols through higher fidelity life predictions.
Provides fundamental understanding of the combined and coupled effects of environmental degradation, elevated temperatures and thermo-mechanical loads on the structural survivability
Capability Development:
The ability to track microstructure damage and failure mechanisms in a structural scale analysis.
The ability to reduce the conputational cost to an affordable extent while maintaining the desired accuracy.
Background and Motivation
The Air Force is actively seeking the capability to build and maintain reusable, in-atmosphere air vehicles operating at hypersonic speeds (Mach 5 and beyond).
Current design and sustainment practice: Simplified component analyses under distinct load cases + knockdown factors to account for the unknowns.
Hypersonic vehicles: High aero-thermo-mechanical loads and environmentally-assisted damage induced by sustained exposure to extreme environments renders current design and sustainment practice ineffective.
Technical Challenges:
Gaining the capability to track damage mechanisms that occur at the microstructure level during structural simulation. –> Efficient, accurate multiscale methods.
Gaining the ability to account for the coupled thermal, mechanical and environmental degradation processes. –> Multiphysics failure models.
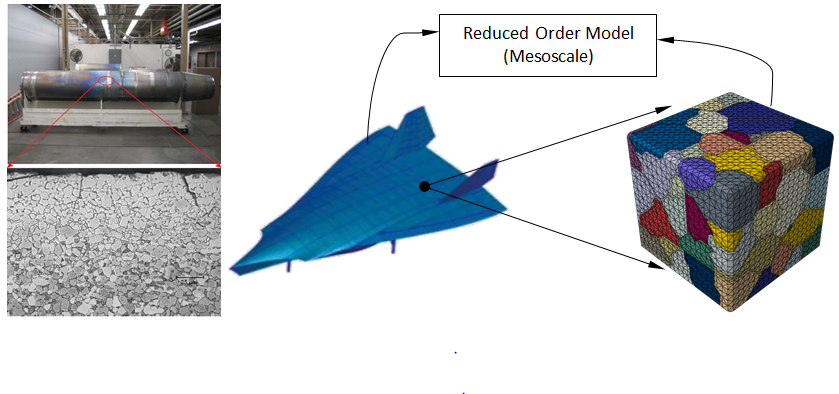
Research Approach
Formulate and implement a multiscale computational framework for modeling the inelastic (i.e., including creep, plasticity) structural response. Crystal plasticity theory will be incorporated and experimental data will be used to verify the accuracy and the validity of the computational framework.
Devise reduced order computational models for inelastic deformation (i.e., plastic deformations, viscous effects and damage) phenomena at the scale of the polycrystal microstructure that can accurately describe the failure response at a fraction of the cost of full resolution microstructure modeling. More deformation features and mechanisms in the crucial location such as the grain boundaries can be tracked.
Investigate damage initiation and accumulation response of titanium alloy structures operating in the presence of high thermo-mechanical loads and sustained thermal environments. The investigations will be conducted on the model material of high temperature titanium alloy Ti-6Al-2Sn-4Zn-2Mo-0.1Si (Ti-6242S).
Assess the computational framework by experimental validation and computational cost evaluation.
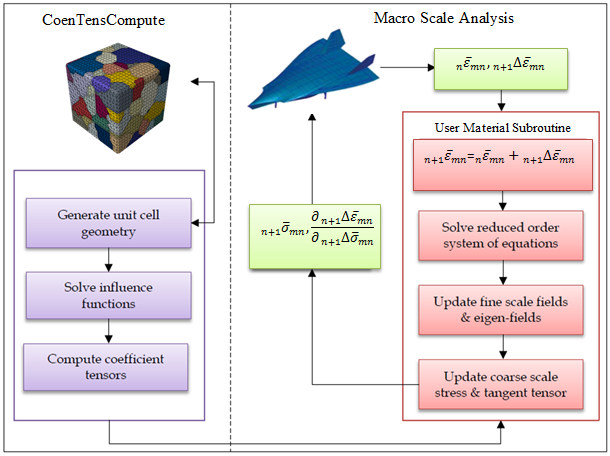
CPFE Simulation based on High Fidelity Microstructure Model
High Fidelity Microstructure Reconstruction:
High fidelity Microstructure is crucial to accurate simulation results and details at grain boundaries.
Discretization work flow: DREAM3D –> Parallelized Polycrystal Mesher (PPM) –> Abaqus.
Ti6242S: Near alpha (HCP) alloy with approximately 5% beta phase (BCC) by volume fraction and no lamellar colonies detected.
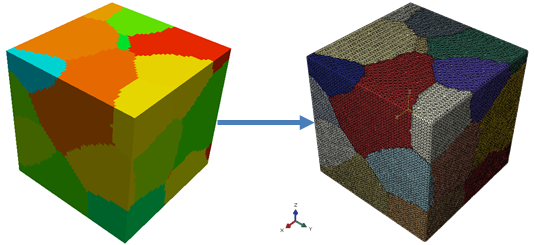
Crystal Plasticity Finite Element Simulation:
Crystal plasticity finite element (CPFE) method will be employed.

Reasonable results compared with reference experimental data.
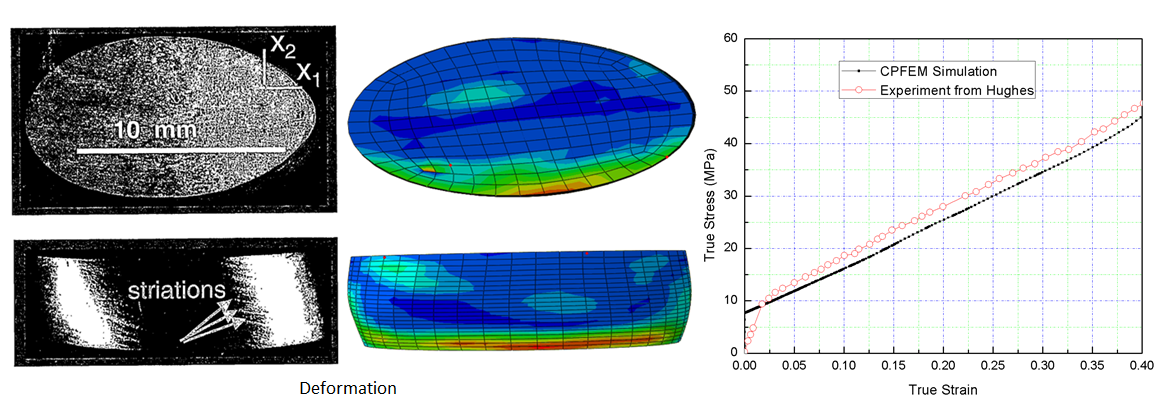
Reduced Order Crystal Plasticity Modelling
Eigendeformation-based reduced order modeling (EROM) will be employed. Target model order reduction is three orders of magnitude. (i.e., from O(5-7) to O(2-4)) degrees of freedom.
A hierarchical sequence of reduced order models with varying fidelity is generated. The computational complexity of the lowest fidelity model is similar to the viscoplastic self consistent formulation. The most comprehensive model coincides with the CPFE model.
Currently implementing the EROM approach for small strain condition.

Eigenstrain of each part is calculated from reduced order system equations.

The EROM formulation will be extended to large deformations.
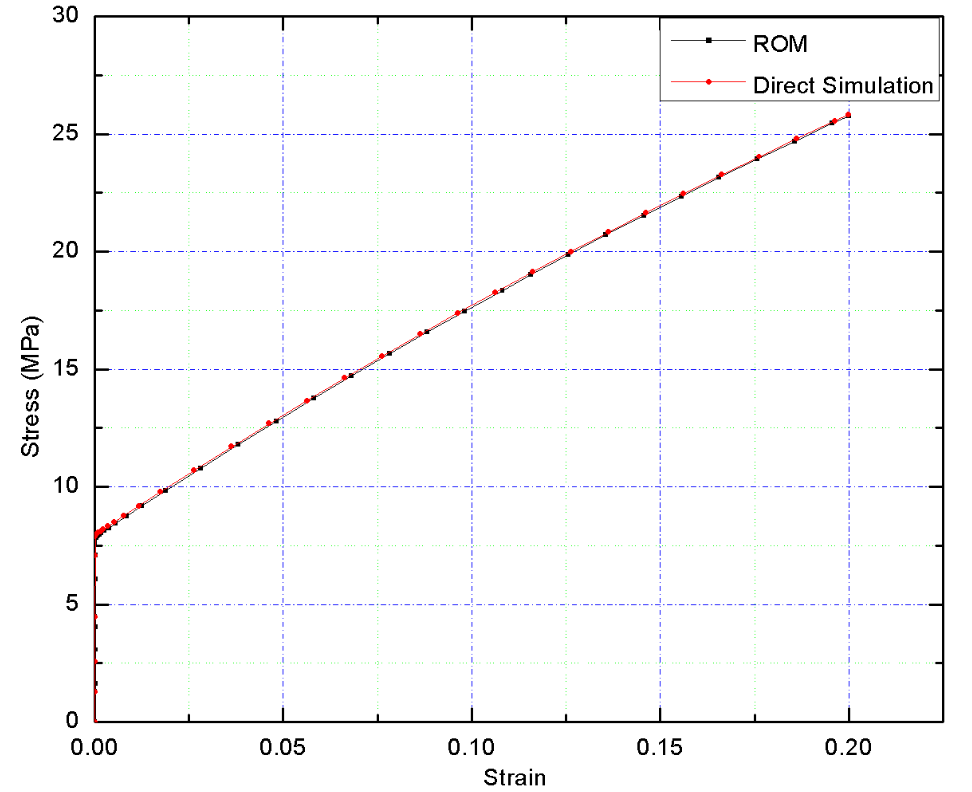